Pioneering technology of the present and future
From medical technology to the semiconductor industry - laser systems offer precision, efficiency and versatility. We integrate systems and develop quality control for our customers.

Laser technology has developed into an indispensable tool and is now present in a wide range of industries and application areas. From medical technology to the electronics industry and the semiconductor sector - laser systems offer precision, efficiency and versatility.
Lasers can process a wide range of materials, including metals, plastics and glass, and offer numerous advantages over traditional methods such as mechanical cutting, punching or milling. For thin materials or complex shapes in particular, lasers offer a safe and fast manufacturing method. As laser processes do not require direct contact with the material, tool wear and maintenance costs can be reduced.
Laser processes allow maximum precision in the micrometre range, minimize material losses and can therefore increase the quality and flexibility of production. The systems can be easily integrated into automated processes and take over central production processes such as precision cutting, welding or surface treatment. Other applications include material processing such as drilling or the inspection of components.

Precision
Precision
Extremely fine details can be processed by laser.

Interdisciplinarity
Interdisciplinarity
Combination of mechanics, electronics and software for innovative solutions.

Sustainability
Sustainability
Resource-saving production and durable products.

Material protection
Material protection
Reduction of material waste, deformation or damage.
Precise and versatile solutions for numerous applications
Cooperation with market leaders
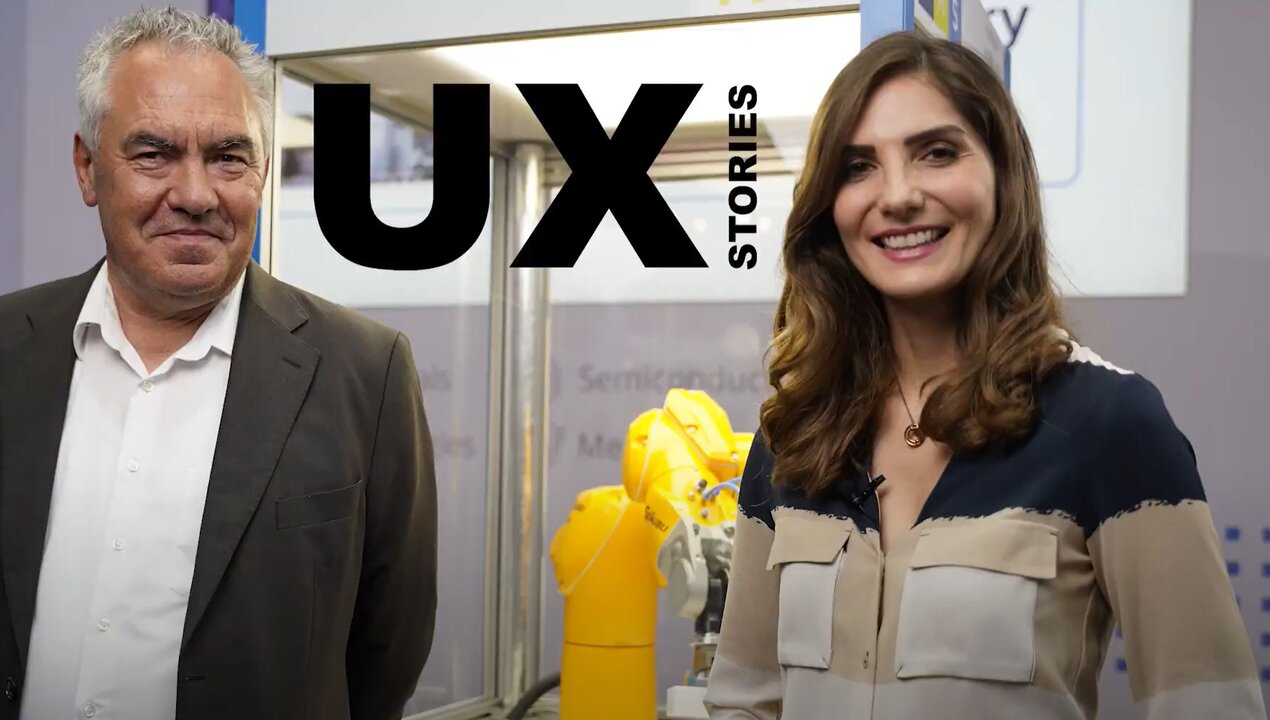
Together with TRUMPF, we have implemented automated manufacturing processes in the field of medical technology and precision engineering. The first case study required a solution for medical implants. By using certain lasers, the active ingredients in the implant are not damaged and can still be cut with high precision. In the second case study, we implemented reliable laser welding processes for a customer instead of screw processes.
Step by step to a successful solution
1. determination of requirements and process analysis: Workshops are used to record an analysis of requirements and materials.
2. Selecting the right laser technology: Determine the laser source (CO2/fiber/solid-state or diode laser), define performance parameters (laser power, beam quality and pulse duration) and determine the provider (tailor-made systems, cooperation with market leaders).
3. Integration in production: Laser processes can be easily automated with robots or CNC machines. This increases efficiency and reduces errors.
4. Test phase with parameter adjustment: Commissioning of the automated processes under control of the previously defined requirements.
5. Monitoring/inspection: Sensors and monitoring systems to control laser processing in real time. The installed inspection systems allow us to continuously monitor the process and optimize the process and product parameters using modern software.
